The increasing use of electronics in the automotive industry has led to the requirement for more testing. Learn more about the new testing equipment available today…
By Sneha Ambastha
The infamous Toyota global car recall that happened between 2009 and 2011 is still fresh in the memory of those in the automotive industry. In this widely reported case, drivers felt the car suddenly accelerating even when the pedal was not in use. Archan Mudwel, technical marketing engineer, National Instruments, says, “Toyota initially recalled the cars claiming it to be a problem with the floor mat design. Subsequently, the car giant claimed that the problem was due to the mechanical sticking of the accelerator pedal. It finally had to recall cars back for the third time for problems traced to the anti-lock braking software.” Many of the electronic systems used in cars today are critical, with the passenger’s safety at stake. This underlines the importance of using good testing equipment in the automotive industry.
The automotive industry has become very competitive in the past few years. The competition is not just with respect to new technologies but also about overall performance, cost and safety. If we set aside cost for a while, both performance and safety demand thorough testing of the different aspects of an automobile, like safety and driver aids (emergency call system during accidents in heavy traffic), in-vehicle networks (CAN, optical fibre and RF connectors/cables), intelligent transport systems or ITS (vehicle-to-vehicle/V2V or machine-to-machine/M2M communication networks, etc), electromagnetic interference (EMI/EMC, interface hunting, etc) and wireless connectivity (in compliance with standards like LTE, 2G, 3G, Bluetooth, Wi-Fi, AM, FM, DAB, RDS, etc).
Mudwel says, “Testing is required at the end of the production line for various automotive components, which range from injectors and fuel pumps to infotainment systems, often including remote keyless entry. There is a need to also test and validate the various control systems in the vehicle like engine control, body control, active suspension, anti-lock braking system, etc.”
Information for decision makers
Every brand has its own test requirements and standards. This might raise the need for customised test equipment. Gautam says, “Wireless applications usage, miniaturisation and complexity in automobile electronic components demands precise, accurate and reliable testing. A test equipment manufacturer needs to be innovative, flexible and ready to customise its equipment to meet the challenging testing requirements of customers.” To this, Mudwel adds, “The customers should try and look for an open system which can allow them to integrate a lot of third party hardware and software to avoid hassles in the future, when they later integrate newer technologies from different vendors. For example, customers often want to incorporate simulation models from third party environments, which specialise in a specific kind of simulation. This may be because they are easy to use or that the teams at the customer’s end are familiar with the tool.” He further says, “The buyers should also be looking for systems that are scalable and can address the changing requirements of the automotive test industry to protect their investments.”
Challenges to be faced
The industry faces challenges at different levels, starting from the supply chain to the design of the test equipment. The first and foremost challenge is the limited awareness about the suppliers of different test equipment in the country. This means that automotive manufacturers contact only few testing equipment suppliers, generally big brands, for any such requirement. Vijay Kumar, general manager, sales and marketing, Qmax Test Technologies Pvt Ltd, says, “Qmax is known as the IC testing and PCB testing company, although it also provides solutions for electronic control unit (ECU) testing. Manufacturers may not know about this and hence not reach out to us for the different ECU tests, functional testers and wire harness test solutions.” The other challenge is that lead times or delivery schedules in the industry are quite short.
There are challenges with respect to the design of the T&M equipment too. The integration of new technologies in vehicles gives rise to the challenge of designing new test equipment for the new test environments. The challenge is to identify the test scenarios. Rahul Gautam, electromagnetic compatibility group, Rohde & Schwarz, explains, “The upcoming automobile technologies like autonomous vehicles, automatic health monitoring, remote shut down, comprehensive car tracking, night vision driving, etc, will require rigorous EMC testing.” He adds, “A vehicle moves in a harsh, ever changing electromagnetic environment with a lot of internal wireless communications. EMC modelling, testing and further qualification as per standards is a critical quality parameter to ensure reliable performance under these stringent conditions. Automobile components and vehicle manufacturers understand the importance of this testing and investing in in-house EMC facilities.”
“The major challenges here are the ever changing requirements and scalability. Conventionally, in automotive test systems, the industry has been focused on signals coming from analogue and digital sensors, but with Vehicle-To-Vehicle (V2V) communication systems, there are RF standards being introduced and, hence, test systems need to scale up,” says Mudwel.
Tech trends
Implementing the optical transport network (OTN) and Ethernet for in-vehicle communication is making automobiles more sophisticated, leading to the requirement of new testing technologies. Then there are a lot of RF components and wireless standards getting integrated into automobiles. The T&M industry is trying hard to build test systems that can thoroughly test all these advanced systems that are being introduced in the auto industry.
Signal transceivers with mmWave frequency: Automated driver assistance system (ADAS) radars operating at high frequencies, typically in the mmWave range, are used to identify the presence of any stationary infrastructure, pedestrian or moving vehicle. Such radars need to be tested for their performance using high-frequency RF transceivers of high bandwidths.
Battery simulators: These are used to test battery management systems, which manage the charge stored in the battery and regulate it during regenerative braking and charging.
Hardware-in-the-loop testing: This means that software in the electronic control units (ECU) is tested without the physical system being controlled, but with only the help of a simulator. The use of a test simulator eliminates the need for multiple testing hardware, minimises the test time and reduces the overall cost.
Pneumatic testing beds: Earlier used by European companies in the aerospace domain, pneumatic test benches are now being used in the automotive manufacturing industry where they not only test performance but also check how parts are fitted, whether or not components attached to an automotive device are sealed and also test its electrical parameters.
“Machines such as the ringout board/inspection system are used during the production stage. All the products to be tested are placed on the test bed, where the tester checks the system’s harness and the missing components, identifies the errors and displays it along with its position. Every component has a label, which does not appear if it has not been tested.”
Other new technologies include the introduction of the USB 3.0 connection in testing devices, as well as advanced triggers to capture intermittent faults. Then there are voltage drop tests with non-grounded measurement of floating inputs and the high voltage range measurements at up to 200V that can be done without the need for any attenuators.
A few new products launched in this segment in the past one year
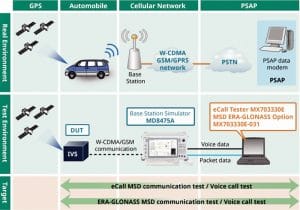
MD8475A signalling testers
This signalling tester from Anritsu is a base station simulator that supports the in-car safety technologies like the emergency calling during an accident in heavy traffic. This simulator supports various wireless communication standards like LTE, LTE-Advanced, W-CDMA/HSPA/HSPA Evolution/DC-HSDPA, GSM/GPRS/EGPRS, CDMA2000 1X/1xEV-DO Rev. A. and TD-SCDMA/TD-HSPA. Its SmartStudio graphical interface supports the setting up of functional and environmental tests. The tester is capable of simulating end-to-end emergency calls as per the given standards with an ability to support multimode terminals.
NI PXIe 5840 2nd generation vector signal transceiver
The PXIe 5840 is a second generation vector signal transceiver from National Instruments’ PXI family, and comes with an instantaneous bandwidth of 1GHz. It has been introduced for applications like automotive radars, vehicle-to-everything (V2X) communication, RF HIL (hardware-in-the-loop), infotainment testing, etc. It works with FPGA based real-time controls and signal processing featuring the radio architecture flexibility with RF class performance. The device combines a small form factor and the fast measurement speed of the test box with the high performance and flexibility of the R&D-grade box instruments.
PicoScope 4000 series automotive diagnostic oscilloscopes
Pico Technology’s PicoScope 4225 and 4425 are the in-vehicle system analysers available in a box. The company claims that they are the most advanced automotive PicoScopes for handling in-vehicle tests in various types of vehicles—hybrid, electric, petrol and diesel. These two-channel and four-channel oscilloscopes are capable of capturing about 400 million samples per second, without affecting sample rates. Their sample rates are fast enough to handle FlexRay and CAN signals, revealing intermittent problems and storing them for later analysis. These PicoScopes have eight times more memory than earlier models, yet are available at the same price.
R&S FSW signal analyser with 1.2GHz bandwidth
The R&S FSW is a signal analyser from Rohde and Schwarz with an increased analysis bandwidth and an internal wideband digitiser. It has been introduced to address the needs of the 5G radio access technologies that require large bandwidth for wideband signal analysis, especially radar signals in cars. The R&S FSW-B1200 is the only signal analyser in this series that has been released lately for the 1.2GHz bandwidth analysis option. It enables wideband amplifier characterisation and R&D for next-generation mobile standards in the band range of 28GHz to 39GHz for 5G technology. On the other hand, for the analysis of applications with a band range more than 1.2GHz and up to 2GHz, the R&S FSW-B2000 option can be used along with an external digitiser.
MT1000A Network Master Pro
The MT1000A Network Master Pro from Anritsu is a battery-powered, multi-function, in-vehicle communication network tester. This compact, lightweight instrument is an all-in-one field transport tester that supports testing of networks from 1.5Mbps to 10Gpbs. It is able to toggle between the traditional optical time domain reflectometer (ODTR) output and graphical summary. It can test multiple wavelengths with a single unit, and can generate PDF and XML reports for the documentation of the tests results.
R&S SMW200A vector signal analyser
Vehicle-to-vehicle communication that supports radar technology needs a system that can generate wideband signals in line with communication standards like IEEE 802.11 ad and 5G. The R&S SMW200A is a vector signal generator from Rohde and Schwarz that offers an internal modulation bandwidth of 2GHz. Its wide baseband generation option through R&S SMW-B9 enables the generation of two independent wideband signals of modulation of up to 20GHz using just one instrument. It is supposed to support challenging applications in the wireless communication, aerospace and defence segments. It is capable of directly creating candid waveforms like UFMC, FBMC, GFDM and f-OFDM, enabling users to understand and analyse the design challenges.
MT8870A universal wireless testers
Anritsu’s MT8870A is a universal wireless tester designed for the high-volume production of wireless modules. The company claims that its ability to operate in a non-signalling environment makes it suitable for fast testing not only in production work but also in calibration, validation and other tests related to the various relevant standards. It has about four transceiver test modules, with an inbuilt signal generator and a signal analyser on each for RF tests. The tester has a modular design with up to 16 high-performance RF ports in one small chassis.
PXIe 8510 vehicle multi-protocol interface module
PXIe 8510 is a six-port NI-XNET interface that provides a flexible architecture that supports multiple protocols. This multi-protocol interface module from National Instruments is a controller area network (CAN) that can also function as a local interconnect network (LIN) interface with the hardware selection option. It can be used in real-time applications that demand high-speed manipulation of 100 CAN frames and signals like in rapid control prototyping, hardware-in-the-loop (HIL) simulation, bus monitoring, automation control, etc.
NI SLSC 12001 chassis with SLSC modules
National Instrument’s SLSC 12001 is a chassis with 12-slot Switch Load and Signal Conditioning (SLSC) modules that enables the host system to communicate and configure the SLSC modules. Along with the SLSC 12001 chassis, there is a wide variety of SLSC modules from NI that fit in this chassis for the various signal conditioning requirements existing in the automotive industry. The customers can design their own modules as well as for their clients’ requirements, and use them within the SLSC framework.
The future of testing in the automotive sector
Going forward, vehicles will integrate more and more electronics, eventually increasing the need for better testing equipment and standards. Gautam says, “Just like any other electrical device, a vehicle and its components are required to meet Indian EMC standards laid out by ARAI (Automotive Research Association of India).”
However, testing has two important phases—standalone testing and life cycle testing. Life cycle tests, endurance tests and other such tests are quite expensive and are of no use if not utilised properly. Usually, companies have centralised labs to carry out these tests but if they do not have such a provision in-house, then they will have to spend a lot to get this done by a third party. In order to avoid this, such tests should be centralised and integrated, while standalone testing should be reduced.