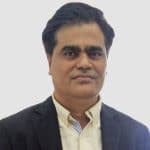
Subhash Pawar supports companies that have aggressive plans for India. As the director of Volga Innovations, a distribution company that provides products for the LED industry, he is confident that Volga’s good quality and affordable products will help it gain a good market share in India in the coming years. During an interaction with Shruti Mishra, business journalist from Electronics Bazaar, he shares his thoughts on how ‘Make in India’ and the growing inclination of customers towards quality products is proving fruitful for his business.
EB: What are the products that Volga Innovations supplies to the Indian LED lighting industry?
We primarily focus on indoor LED lighting. In India, the products that we offer and support include diffuser solutions, sidelight solutions and drivers. On the optics side, we support a company called Herculux and for indoor LED diffuser solutions, we work with Sewon. We also have thermoplastics from Nanoplus Tech, which are being used as a replacement for aluminium now.
EB: What is the current market share of Volga Innovations in India?
Currently, our turnover is around US$ 4-5 million in India. In 2016, there was a dip but 2017 has been a good growth year for us. Globally, India’s overall share of the LED market currently is less than 10 per cent, whereas China contributes to more than 50 per cent of the products manufactured. So, if not 50 per cent, we hope to help drive India’s share to 20-25 per cent of the global LED market. We are planning to achieve this target with our quality and well-tested products, which we offer at a good, reasonable price. That is why we are sure that we will get a good market share.
EB: So, as a distributor, how much potential do you see in the Indian market?
The Indian market is currently very small but we estimate that in the near future it will grow much bigger. This is because China’s overall cost of manufacturing is going up as its standard of living is improving. That is impacting the product’s cost as well. I would say that now, it’s no longer feasible to manufacture products in China. In the next three to five years, we will see some major changes. Under the ‘Make in India’ programme, a lot of Chinese and other foreign companies are thinking of manufacturing in India. Although this is happening gradually, it’s making a difference already. So that trend is going to impact us positively, because every company that starts manufacturing here will need components. That means our business is definitely going to grow. I see this trend continuing for the next five years at least.
EB: Have you participated in any of the government tenders as yet?
As of now, we haven’t, because the government is primarily focusing on mass outdoor products like streetlights, which at the moment is not our prime focus area. Maybe, in the future, when the government shifts its focus to indoor lighting, we will participate in government tenders.
EB: Two major economic transitions happened in 2016-2017—demonetisation and GST. How have these impacted your business?
For us, demonetisation had a limited impact for about one or two months but we didn’t face any major problems. So was the case with GST. Frankly speaking, we didn’t see any negative impact of these two on our business. In fact, in 2016-2017, our revenue has almost doubled from the previous year. During the period from January to November 2017, our sales have grown by 70 to 80 per cent.
EB: How do you select your principals?
The first and foremost factor is the quality of their products. The second thing we look for is how the company is structured—whether it has professional management or the will to scale up, and how bullish is its management with regard to India. As a lot of things are changing now, foreign companies have started taking India seriously. India is the only market globally which is growing at a fast rate along with the large markets. Companies have realised that the country has a lot of potential and therefore they want to come here. We like to represent the companies that are keen to work in India.
EB: What sets you apart from your competitors?
The difference between other distributors and Volga is we are not just a distribution company but also a solutions company. We don’t just trade; rather, we take the product from the concept to the final product. Our technical team helps customers in designing also. Once the product is designed, it goes to the market. After this, if there are any productivity issues, we also help in overcoming them.
For instance, most of our competitors are supplying polycarbonate sheets that are being used in very limited applications in lighting. The market share for these sheets is shrinking now, because these are getting replaced with PMMA or PS materials.
In addition, India is also a price-sensitive market. People want excellent quality at a reasonable price. And that is where we have positioned ourselves. We offer a very good quality product at a very reasonable price.
EB: How are you promoting your products?
We participate in a large number of exhibitions and expos. We primarily target Tier I companies and we also look at selling to the OEMs. Now, we have expanded our reach to Tier II and Tier III customers as well. So, we would like to use a medium that can extend our reach into these two segments. Apart from these, we are also focusing on some technical seminars to which we can invite customers and explain the advantages of our products. We haven’t started doing online promotions but, hopefully, in 2018, we will.
EB: Do you also engage with any of the resellers?
No, because our products are not meant for resellers.
EB: What’s your priority – the design team or the purchase team?
I think the design of a product is critical. If you have a good product but are not able to address the customers’ needs, then the product is of no use. Selection of vendors is something we do ourselves. So, at Volga, we give first preference to the design team, then comes the sales team and after that, the purchase team.